第3章 滾柱活齒減速器的設(shè)計及計算機輔助分析
3.1引言
本章在活齒傳動理論分析的基礎(chǔ)上络跷,針對井下驅(qū)動螺桿泵采油系統(tǒng)的實際技術(shù)要求,設(shè)計最大外徑114mm谴眶、傳動比為9俺阻、工作井深1000m的滾柱活齒減速器以滿足油田生產(chǎn)需要。
首先宰蘸,給出根據(jù)滾柱活齒傳動的運動條件和強度條件設(shè)計減速器的方法督靶,并根據(jù)這些約束條件初步確定減速器的參數(shù)。為準確驗證所設(shè)計的減速器能否實現(xiàn)預(yù)定的設(shè)計要求捂臣,本章擬采用有限元分析的方法铃挠,針對減速器關(guān)鍵零件進行靜力學(xué)分析和模態(tài)分析,以驗算其強度是否滿足要求堡掏,確定輸入应结、輸出軸正常工作時能否受激共振。
同時泉唁,為避免樣機加工后發(fā)現(xiàn)問題而造成損失鹅龄,縮短設(shè)計周期,在樣機設(shè)計完成后亭畜,擬采用虛擬樣機仿真技術(shù)對其進行運動學(xué)仿真扮休,以驗證其能否實現(xiàn)確定的相對運動。仿真成功后拴鸵,繪制出全部零件圖和裝配圖并加工樣機肛炮。
3.2 減速器結(jié)構(gòu)的設(shè)計
為簡化樣機結(jié)構(gòu),將波發(fā)生器與輸入軸設(shè)計成一個零件宝踪,統(tǒng)稱輸入軸。將中心輪固定碍扔,選擇輸入軸和輸出軸旋轉(zhuǎn)方向相同瘩燥。由于波發(fā)生器部分屬偏心結(jié)構(gòu),工作時要承受很大的徑向力不同,為改善支承的受力情況露揽,采用雙排相差為180°的滾柱活齒結(jié)構(gòu),不但使慣性力和慣性力矩完全平衡酵吴,而且保證整機的嚙合力和嚙合力矩平衡屏部。
由于中心輪內(nèi)齒面要同時與相差為180°的兩排活齒嚙合而且中心輪的齒形加工采用線切割工藝,所以中心輪沿軸線上各截面形狀應(yīng)保持一致。確定采用的結(jié)構(gòu)后藐捉,根據(jù)運動條件和強度條件初步確定減速器的具體參數(shù)铭歪。
3.2.1 運動條件
3.2.1.1 中心輪理論齒廓曲線不頂切條件 由于中心輪理論齒廓曲線是滾柱活齒中心運動軌跡的等距線,所以當(dāng)滾柱活齒中心運動軌跡的最小曲率半徑ρmin≥r2時氛玛,活齒可以順利地通過中心輪的齒頂搀薛;當(dāng)ρmin≤r2時,中心輪的理論齒廓曲線要發(fā)生頂切現(xiàn)象蹂勺,從而使傳動終止稻填,據(jù)此可寫出中心輪理論齒廓曲線不頂切條件:
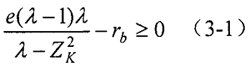
式中e——波發(fā)生器偏心圓的偏心距;
λ——激波系數(shù)携帘,λ=(r1+r2)/e恰壁;
r1——波發(fā)生器半徑;
ZK——中心輪齒數(shù)旨椒;
r2——滾柱活齒半徑晓褪。
連續(xù)的齒廓曲線有傳動平穩(wěn)、參與嚙合的齒數(shù)多等優(yōu)點钩乍,所以設(shè)計活齒傳動時辞州,一般總是希望得到連續(xù)的齒廓曲線,即使之滿足式(3-1)寥粹。
3.2.1.2 偏心距e和徑向間隙c是活齒減速器的重要參數(shù)变过,減速器的結(jié)構(gòu)形式和傳動比不同,偏心距e和徑向間隙c 的值也不同涝涤,其取值應(yīng)按表3-1中的參數(shù)優(yōu)先選取媚狰。
表3-1 徑向間隙c、偏心距e的優(yōu)選值(mm)
偏心距 |
0.65 |
0.75 |
0.85 |
1 |
1.25 |
1.5 |
1.75 |
2 |
2.5 |
3 |
3.5 |
4 |
徑向間隙 |
0.9 |
1.0 |
1.1 |
1.2 |
1.3 |
1.4 |
1.5 |
1.6 |
1.7 |
1.8 |
1.9 |
2 |
偏心距 |
4.5 |
5 |
5.5 |
6 |
6.5 |
7 |
7.5 |
8 |
9 |
10 |
11 |
12 |
徑向間隙 |
2.1 |
2.2 |
2.3 |
2.4 |
2.5 |
2.6 |
2.7 |
2.8 |
2.9 |
3 |
3.1 |
3.2 |
3.2.1.3 滾柱活齒連續(xù)傳動條件 為保證活齒在工作開始位置(中心輪齒頂)傳動連續(xù)阔拳,活齒在與中心輪齒頂接觸的同時崭孤,與活齒架應(yīng)保持接觸。由幾何條件可知糊肠,活齒架內(nèi)圓半徑最大值即活齒工作起始位置連續(xù)傳動條件為:
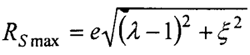
式中 ξ——活齒系數(shù)辨宠,ξ=rb/e;
RSmax——活齒架內(nèi)圓半徑最大值捌养。
活齒架內(nèi)表面和波發(fā)生器外輪廓面之間不應(yīng)該發(fā)生運動干涉湾蝙,不發(fā)生運動干涉的條件為:
RSmin=e(1+λ-ξ)
式中RSmin——活齒架內(nèi)圓半徑最小值。
上兩式聯(lián)立螃妨,可求出活齒架內(nèi)圓半徑RS的尺寸范圍惰绘,見式(3-2)。

同樣方法可得活齒工作結(jié)束位置(中心輪齒根)連續(xù)傳動條件:

式中RMmin——活齒架外圓半徑最小值耐叽。
活齒架外表面和中心輪的齒頂不發(fā)生運動干涉的條件:

式中RMmax——活齒架外圓半徑最大值蟀蛆。
上兩式聯(lián)立友熟,可求出活齒架外圓半徑RM的尺寸范圍,見式(3-3)男沛。

3.2.1.4 活齒架的最小壁厚 聯(lián)立活齒工作起始位置和結(jié)束位置時的連續(xù)傳動條件栓占,可得活齒架薄壁筒的最小壁厚為:

3.2.2 強度條件
3.2.2.1 活齒與波發(fā)生器間表面接觸疲勞強度
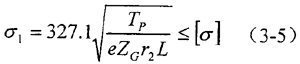
式中TP——波發(fā)生器的輸入力矩,N·m宗恩;
ZG——活齒數(shù)紊尺;
L——活齒工作寬度,m领姨;
[σ]——考慮壽命达吞、載荷等因素的許用應(yīng)力,[σ]=1423MPa荒典。
3.2.2.2 中心輪接觸疲勞強度

式中ρ——綜合曲率半徑酪劫,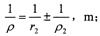
ρ2——取中心輪齒廓曲率半徑最小值,m寺董;
E——彈性模量覆糟,2.06×1011N/m2;
FKmax——活齒對中心輪的作用力遮咖,N滩字。
在齒根附近(拐點以下)嚙合時,綜合曲率半徑ρ中取減號御吞,在齒頂附近(拐點以上)嚙合時麦箍,綜合曲率半徑ρ中取加號。
3.2.2.3 活齒架接觸疲勞強度和剪切強度 剪切強度為:
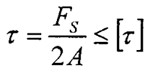
式中A——每個活齒槽的橫截面積陶珠,A≈2r2(RM-RS)挟裂;
FS——活齒對活齒架作用力,N揍诽;
[τ]——許用剪應(yīng)力诀蓉,MN/m2。
接觸疲勞強度:
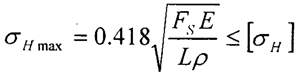
式中E——彈性模量竖枚,2.06×1011N/m2劝讯。
首先根據(jù)上述運動條件初步確定幾何參數(shù),然后采用強度條件校核路棍。經(jīng)分析可知持乌,參數(shù)可行域很小,考慮到波發(fā)生器偏心距e祖匕、徑向間隙c等參數(shù)需圓整為表3-1中的優(yōu)選值,初步確定主要參數(shù)如下:波發(fā)生器偏心距e=1.5mm美域,波發(fā)生器半徑r1= 30mm汪怒,r2=8mm叽渡,活齒數(shù)ZG=9,中心輪齒數(shù)ZK=8杭厘,活齒工作寬度L=60mm酣殊。
3.3 滾柱活齒減速器有限元強度分析和模態(tài)分析
有限元法(FEM)是一種采用計算機求解結(jié)構(gòu)靜、動態(tài)力學(xué)特性等問題的數(shù)值解法隶丁,現(xiàn)己廣泛應(yīng)用于結(jié)構(gòu)锡移、熱、電磁場漆际、流體等分析領(lǐng)域淆珊,成為現(xiàn)代機械產(chǎn)品設(shè)計中的一種重要工具。當(dāng)前奸汇,國際上最權(quán)威的大型商用有限元分析軟件是美國ANSYS公司的ANSYS軟件施符。
進行有限元分析,首先要建立被研究對象的實體模型擂找。ANSYS提供了三種方法創(chuàng)建實體模型:自下而上法(Bottom-up)戳吝、自上而下法(Top-down)和從其他CAD系統(tǒng)導(dǎo)入法。
自下而上法是先創(chuàng)建關(guān)鍵點贯涎,然后依次創(chuàng)建相關(guān)的線听哭、面和體等圖元。自頂而下法是可以直接創(chuàng)建最高級的圖元塘雳,即幾何體素陆盘。當(dāng)用戶定義了一個體素時,程序會自動定義相關(guān)的面粉捻、線和關(guān)鍵點缅含。用戶可以利用這些高級圖元直接構(gòu)造幾何模型。在ANSYS建模過程中杖荤,自頂而下的建模方法和自底而上的建模方法是可以自由組合使用的脓擅,從而使模型的創(chuàng)建更加方便。
另外窥吮,ANSYS提供了與其他CAD系統(tǒng)的強大接口嚣僚,用戶也可以在擅長的CAD系統(tǒng)里建立實體模型,然后把該模型以某一種格式導(dǎo)入到ANSYS中哗搏,一旦模型成功導(dǎo)入后甫沉,就可以象在ANSYS 中創(chuàng)建的模型那樣對此模型進行網(wǎng)格劃分。這些接口程序是由ANSYS公司或CAD供應(yīng)商編寫的軟件酒危。由ANSYS公司可以得到下列軟件的譯碼器似靖;AutoCAD、CADAM败旋、CADKEY和Pro/ENGINEER 录切。
其中值得注意的是ANSYS-Pro/ENGINEER接口炎剿,因為它提供了以執(zhí)行部件為基礎(chǔ)的參數(shù)化優(yōu)化設(shè)計的功能。該功能允許由部件為基礎(chǔ)的參數(shù)化Pro/ENGINEER模型開始蓝角,用ANSYS程序?qū)ζ溥M行優(yōu)化阱穗,并以一個優(yōu)化的Pro/ENGINEER 模型結(jié)束,且仍是以部件為基礎(chǔ)的參數(shù)化模型使鹅。
3.3.1 減速器三維實體模型的建立
無論進行有限元分析還是虛擬樣機仿真揪阶,都要求首先建立減速器的三維實體模型。雖然ANSYS 在有限元分析方面技術(shù)領(lǐng)先患朱,但其在三維實體建模方面并不比專業(yè)的CAD系統(tǒng)方便鲁僚,甚至對于復(fù)雜的實體模型還要借助第三方軟件才能完成。由于滾柱活齒減速器的中心輪和活齒架等零件的實體特征較復(fù)雜麦乞,故考慮采用第三方軟件來完成蕴茴。
工程用三維實體建模軟件主要有Pro/ENGINEER、Ideas姐直、UG等倦淀。其中美國PTC公司開發(fā)的Pro /ENGINEER 是世界上第一個基于特征的參數(shù)化實體建模軟件,其在三維建模声畏、尤其是復(fù)雜曲面的造型方面處于領(lǐng)先水平撞叽。所以減速器擬采用Pro/ENGINEER進行建模。
無論進行有限元分析還是虛擬樣機仿真淤点,我們只需研究與減速器工作直接相關(guān)的波發(fā)生器劣搪、活齒、活齒架和中心輪等關(guān)鍵零件揉远,而忽略端蓋斟迁、端套、軸承等輔助零件衰件,據(jù)此建立減速器三維實體模型及其分解圖見圖3-1和圖3-2邻因。
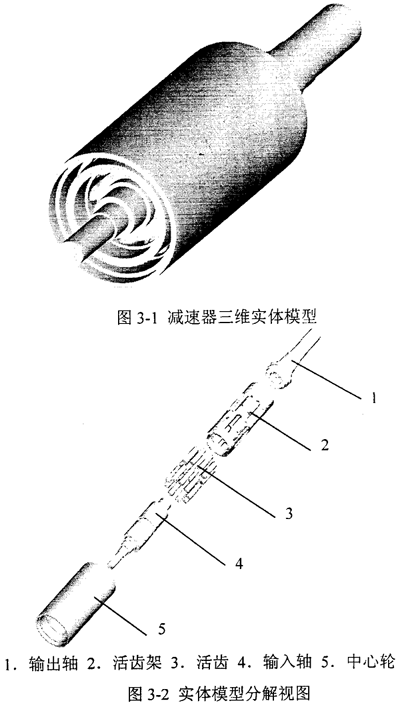
3.3.2 減速器關(guān)鍵件的有限元強度分析
3.3.2.1 活齒架的強度分析 采用平臺為Pentium IV 1.7GHz CPU 、128MDDR SDRAM內(nèi)存擅盏、NVIDIA Geforce2 MX/MX4OO顯卡耽暖、Windows XP操作系統(tǒng)和ANSYS5.7 軟件進行分析求解。
將Pro/ENGINEER中創(chuàng)建的活齒架模型以IGES格式導(dǎo)入ANSYS中纹硼,并作適當(dāng)拓撲修補英胖,以完成預(yù)處理中實體模型的建立。
根據(jù)問題的性質(zhì)和模型的復(fù)雜程度壶缚,選用Solid95單元(見圖3-3)皿港。該單元是三維的20個節(jié)點的結(jié)構(gòu)單元,可以在保證計算精度的前提下允許實體中不規(guī)則的形狀存在溉奕。每個節(jié)點存在三個自由度:X褂傀、Y和Z方向的移動羞酗,可應(yīng)用于塑性、脆性紊服、大變形和大應(yīng)變等問題。
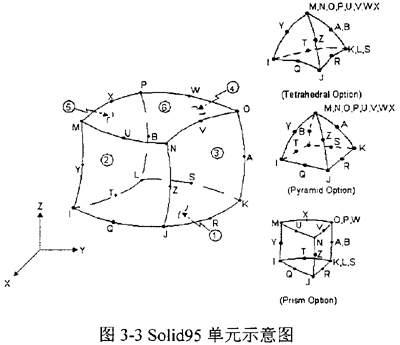
設(shè)定材料屬性為線性各向同性胸竞、楊氏模量為2.06×1011N/m2欺嗤、泊松比為0.3,采用自由網(wǎng)格劃分并設(shè)定劃分網(wǎng)格精度為7。在每個工作活齒所在活齒槽中分別加載4400N卫枝,限制輸出端節(jié)點的全部自由度煎饼,劃分網(wǎng)格并加載后的有限元模型見圖3-4。求解后校赤,在后處理中各節(jié)點的總位移等值圖見圖3-5吆玖,最大位移在節(jié)點688處,值為0.71μm马篮。各節(jié)點的綜合應(yīng)力等值圖見圖3-6沾乘,其中最大綜合應(yīng)力在節(jié)點69處,大小為599846N/m2诽泪,小于許用應(yīng)力杰赴。
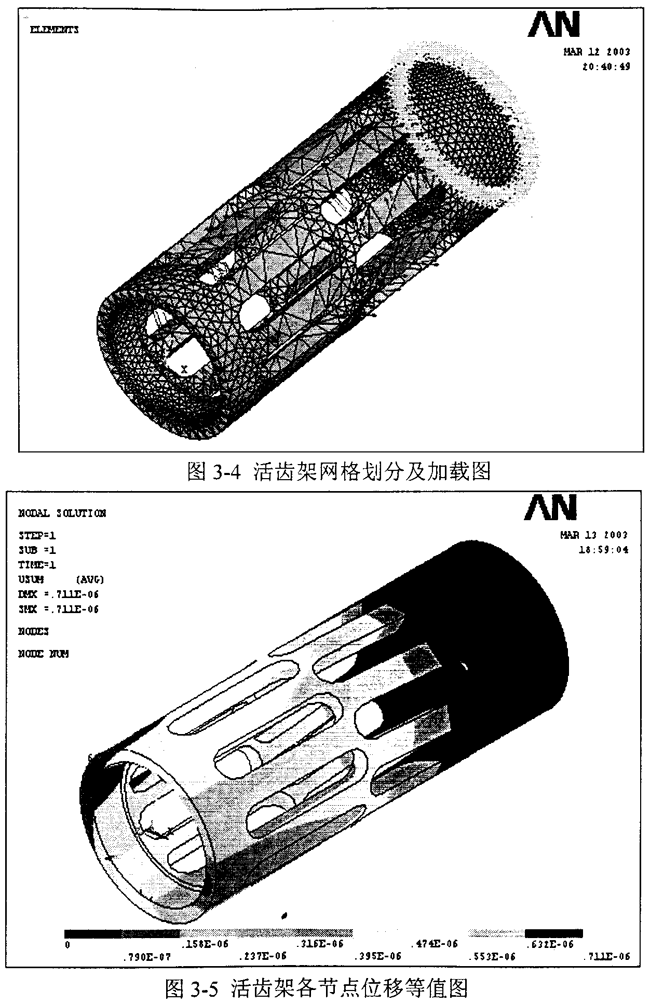
3.3.2.2輸入輸出軸的強度分析 同樣將Pro/ENGINEER中創(chuàng)建的輸入軸和輸出軸模型以IGES格式導(dǎo)入ANSYS中,并作適當(dāng)拓撲修補挂闺,完成預(yù)處理中實體模型的建立便金。
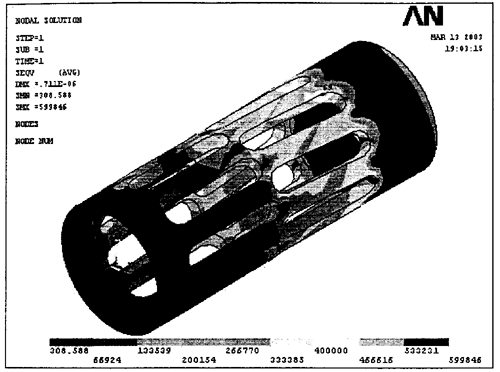
全面考慮計算精度與計算機資源,選用Soild45單元(圖3-7 )轮贫,該單元有8個節(jié)點断克,每個節(jié)點有X、Y和Z三個方向的自由度蛛跛。同樣設(shè)定材料屬性抑琳,采用自由網(wǎng)格劃分并設(shè)定劃分網(wǎng)格精度為9。對輸入軸限制輸入端節(jié)點的全部自由度膝班,在另一端施加工作扭矩头位,劃分網(wǎng)格并加載后的有限元模型見圖3-8。求解后庇晤,得各節(jié)點的總位移等值圖見圖3-9虱硝,最大位移在節(jié)點420處,值為0.254mm厕氨。
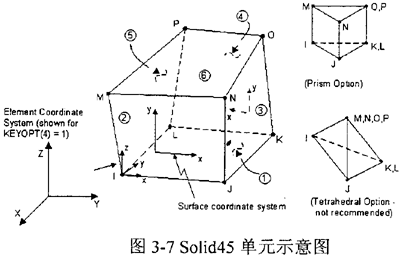
各節(jié)點的綜合能力等值圖見圖3-10进每,其中平均綜合應(yīng)力為75043N/mm2,遠小于材料的許用應(yīng)力。
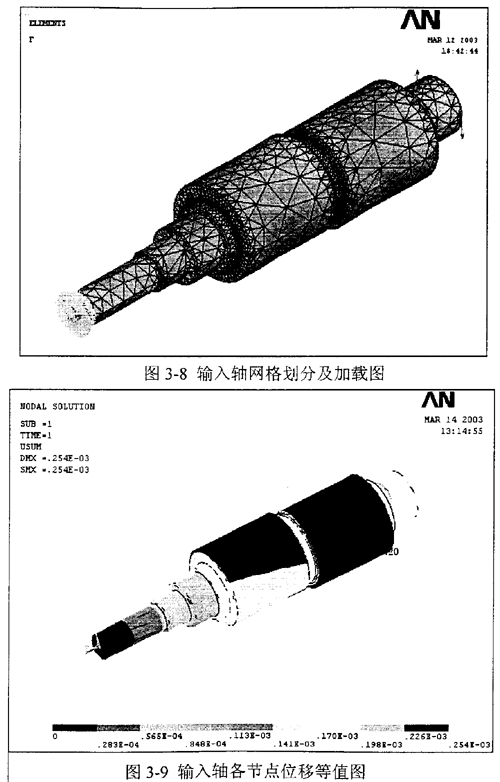
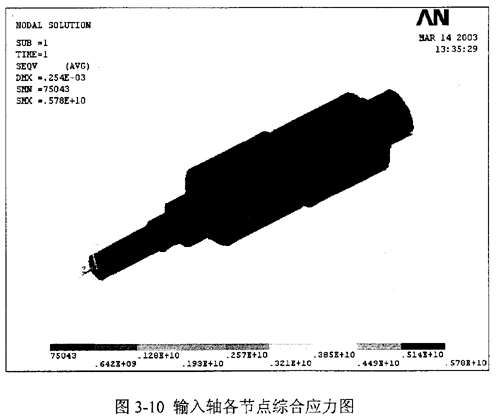
同樣命斧,輸出軸劃分網(wǎng)格并加載后見圖3-11田晚,各節(jié)點位移圖和綜合應(yīng)力圖分別見圖3-12和圖3-13嘱兼。查詢可知輸出軸了大位移在節(jié)點49處,位移值為0.333mm贤徒。平均綜合應(yīng)力為1.5MN/mm2,遠小于許用應(yīng)力芹壕。
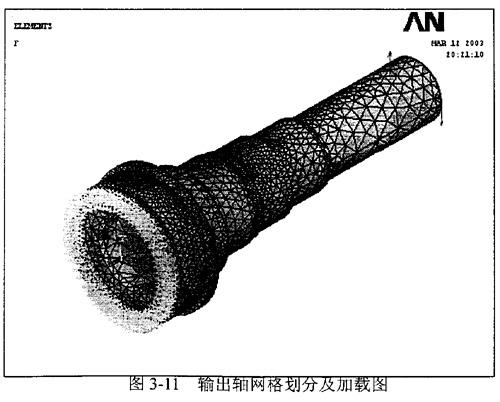
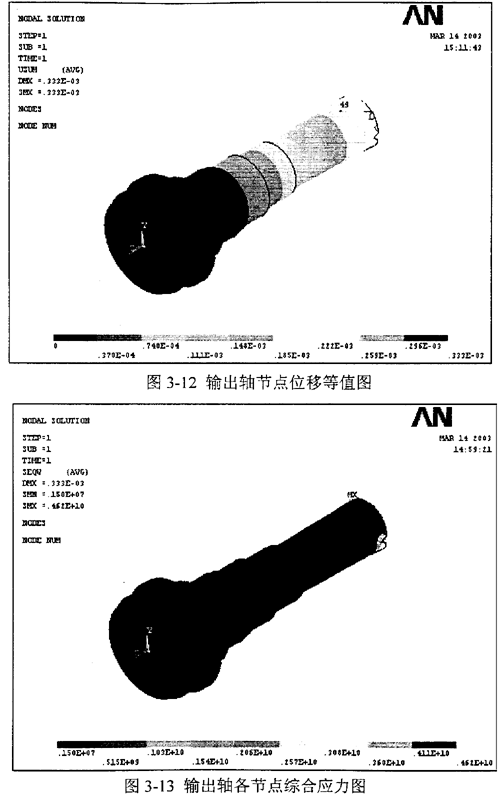
上一頁
下一頁
|